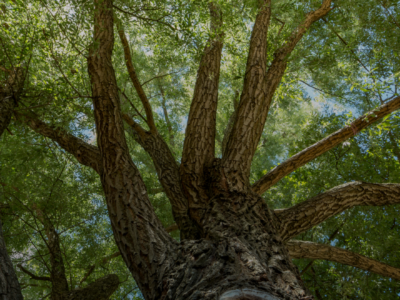
Technical Library
Cut & Sliced Veneers
We pride ourselves on manufacturing and supplying the finest wood floors available on the U.K market. This section discusses how we’re able to confidently sell our products and give you peace of mind that you’ve got a high quality floor. For more information on our manufacturing processes please call 01666 504 015.
Engineered wood flooring is now accepted as the preferred, sustainable choice for wood floors.
There are numerous reasons why engineered wood flooring is such a popular choice. For example:
- Stability – Quality engineered flooring will not twist, warp and cup like solid wood, it will not react as severally to the rises and falls in temperature.
- Quick & easy installation – Providing you’re not using under floor heating there is normally no need to acclimatise engineered flooring prior to fitting (unlike solid wood which requires at least two weeks).
- Sustainability – We can manufacture between 3 to 4 times more wood flooring from the same tree and use faster growing trees for the plywood like birch and eucalyptus. On our wider wood floors we use the cut waste to finger joint a middle layer and a back layer to create a stable very wide (340mm) engineered oak floor using 100% oak, this can be seen on our E110 oak floor.
There are different methods to creating the solid top layer of an engineered floor board. The two main types are discussed in the following sectons:
Cut Veneer
The tree is normally air dried, and then cut into thick planks. These are kiln dried and sawn by a band saw, creating what we call the wear layer or top layer on an engineered board.
This layer is carefully machined to create a high quality veneer that is smooth and consistent with its dimensions. We also use this process to “Quarter Saw” our logs creating products such as our engineered parquet TW-E952
This process produces a board that has the same feel and grain appearance of a solid board.
The veneer is then coated before being laid on top of a quality-approved pre-cut piece of multilayer plywood. These boards are then loaded into a cold hydraulic press.
Once this is completed the boards are ‘balanced’ in a kiln to ensure that the level of moisture in both the solid top layer and plywood is the same before being processed.
This is done in a profiling machine and finishing line and then packed into specialist cartons for total protection.
The images above show a flat cut veneer (left) and a quartered veneer (right).
Sliced Veneer
During this process, the log is soaked in hot water of up to 100 degrees centigrade which essentially boils the log. This is done in order to make the grain soft and sometimes a chemical is added in order to soften the timber further.
Once soaked and softened the wood is then ready to be placed on a machine where it is sliced.
The large veneer slicing machine ‘peels’ the veneer back as the log is turned. This process is visually similar to a roll of carpet being unravelled.
This process understandably produces a lot less waste, as it peels each layer continuously from 1mm to a maximum of 6mm thickness.
Slicing the veneer using this process can make the oak a darker colour. There is also very little heartwood in sliced veneers, as the machine doesn’t cut towards the centre of the tree.
Sliced veneers are liable to splitting in their later life, especially when used over underfloor heating systems. This is because during the heating and softening process, the cell structure has been altered through expanding the wood with water-which needs to be done in order to slice the log.
The veneers are finally kiln dried, which takes the remaining moisture out of the wood- but the finished cut veneer will have a more ‘open’ look and feel to it.
Sliced veneers can alter over time as environmental conditions can often split the grain open. This could eventually cause it to splinter. For this reason we avoid this method of manufacturing an engineered wood floor.
A rotary cut veneer.
Join our mailing list
Receive the latest news, offers and inspiration straight to your inbox.