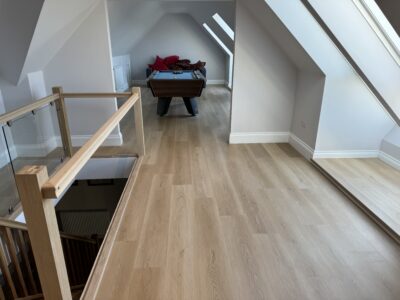
The Solid Wood Flooring Company
Wood Flooring FAQ’s
Below is a selection of the questions we get asked most of the time. If you wish to add to this list, please let us know so we can continue to add content. It is not a definitive document as we will never be able to cover every eventuality on wood flooring because there will always be individual circumstance that we have yet to come across.
Wood flooring and sub floors:
There are many types of subfloors from those where Edwardian and Victorian houses have an airspace underneath joist to new concrete slabs and cement screeds.
The moisture level must be less than 2% and any screed in a normal temperature of around 18 degrees will take one day per 1mm to dry out. A 70mm screed for example will take 70 days
Any type of underfloor heating system must be tested and commissioned before you consider installing any timber floor. You then turn it off before installing any floor.
The slab under these types of systems must be fully sealed with a DPM sheet or high-quality liquid DPM to fully seal the area underneath and up to the top of the cradle system. This will prevent the moisture in the concrete slab affecting the timber in the cradle system and also the floor. Concrete slabs in new builds will take 10 years to dry out.
This type of screeds will have salts and other chemicals in their mix and are normally âpouredâ or âpumpedâ in. As they settle and dry a âlaitanceâ will form on the top. This must be removed within 7 days so that the resulting screed can dry out. If left the laitance will seal in the moisture in the slab and eventually crack and then moisture will come out and affect any timber very badly. The timber is likely to twist and warp. Liken it too custard that has been left for a couple of days where a skin forms on the top and the bottom is âmushyâ.
The best way is to remove the old floorboards and then check the joist and the base floor and make sure that the bricks or other method of allowing air to circulate underneath as free form debris and other obstacles. You can then add insulation between the joists using âhangersâ and then fix a 20mm structural board direct to the joists. An alternative method is to screw marine plywood to the joists and then fully bond a 15mm engineered board which can also be herringbone or chevron. Parquet herringbone and chevron cannot be fitted to joist as it needs a plywood or chipboard subfloor.
Our Wood flooring meets all the requirements of BS6399 â Part 1 for load bearing. We can also confirm that our Engineered and Solid Wood floors comply with BS6399-1:1966 Table 1, Section 3 and specifically Museum Floors and Art Galleries for exhibitions.
Our boards also comply with Clause 5.1.2 âUniformly Distributed Loadsâ and clause 5.1.3 âConcentrated Loadsâ.
You will need to use a structural floorboard (i.e. 20mm thick with a multi-layer backing) with joists 300-350mm centres. These boards can be secret screwed or nailed into place. Please note, parquet is not suitable for fitting direct to joists.
This needs to be repaired and the best way is to use a Schonox product that contains strengthening fibres. You can see this in the case study on York house here
As a general rule, it is better to fully bond (glue) the wood floor to the subfloor. However, there may be some rare instances where floating is required (i.e. youâre using a click-lock floor). For more information please speak to our experts to discuss your project specifics.
Ultimately this will depend on the usage the floor will get and what you are expecting from the floor. We offer either UV Oiled, Lacquered or Hard Wax Oil finished to our products. Some hardwoods work better with particular finishes (i.e. Walnut is best Hard Wax Oiled). Oak is more versatile in terms of what it can be finished with, however, most of our clients are very happy with our UV Oiled range as it gives the benefits of ease-of-repair of an oiled floor with the added surface protection as a lacquered finish.
Yes, wood flooring can be fitted in any part of your home. Remember that wood flooring is a natural product and will react differently compared to man-made or stone tile options. Discuss care and maintenance advise with our experts prior too fitting in high spillage areas.
There are a number of advantages in choosing engineered boards instead of solid. These are as follows:
It is significantly more sustainable and friendly to the environment as around five times the amount of hardwood (e.g. Oak, Walnut, Maple etcâŚ) to produce a solid board compared with an engineered board.
Engineered wood flooring is suitable for use with under floor heating â see our UFH guide for more information.
Engineered wood floors are more stable than solid, are less likely to move and warp
Engineered wood floors can be made wider and longer than solid boards
Engineered wood floors can be fitted with no acclimatisation period providing there is no under floor heating where the boards are being fitted.
It is possible to install a new wood floor on top of existing tiles; provided they are sound, level and free from dirt/grease/grime. You may need to lay a ply over the top of the existing tiles to ensure a flat surface. These specifics will need to be discussed with your fitter.
When you see a wood floor described as âUnfinishedâ that means we have not applied any protective coatings to the boards. This gives you the opportunity to lay the floor and then apply whatever products you wish to protect the floor and give it any colouring desired. Our team are able to assist in discussions about some of the options available in terms of on site finishing products.
The difference between herringbone and chevron parquet is how the boards join together. A chevron parquet end in a point as the ends of the boards are cut at typically either 30, 45 or 60-degree angles. A herringbone parquet on the other hand does not have an angled cut, rather the pieces are rectangular, and one lays across the top of another creating a stepped pattern.
Solid boards need to be acclimatised for 14 days before fitting. This can be done by following the guidelines below; Store the boards in the environment in which they are to be laid. Leave the boards in their cartons, with both the top and bottom end open. Store at least 500mm away from any wall Support the Cartons off the ground at a minimum of 400mm along the length.
Delivery is within three working days following receipt of payment. This is an industrial delivery, therefore someone must be present to unload, check and sign for the goods.
We offer a next working day service for our Cleaning & Maintenance products providing you order before 11AM.
We do not stock transitions/trims; however, for large projects we may be able to craft an accompanying transition/stair nose/skirting etc⌠providing the specification is detailed and discussed prior to ordering.
In fact, with our engineered boards you would not normally need transitions thresholds or anything else and they are a trip hazard as well. It is easy to router out part of the board to fit carpet to and if it butts up to tiles there is normally no need for an expansion gap as long as you use our SW890 adhesive and have a gap around the perimeter where the boards are covered by skirting.
We can make matching stair noses and in some cases are able to supply solid oak matching stairs if you have a glass balustrade.
Grading is a way of outlining the scope of visual characteristics of the wood floor in terms of grain pattern, knotting, splits etc⌠We use an alphabetical listing from A-F grade, combinations of these are used to show the range possible within a product. From a description we also describe these with the terms: Prime, Select, Character, Mixed and Rustic. For more information please see our Grading of Wood Flooring document
Yes â We encourage our customers to see a sample of the product before you order. Samples are free and we will send up to 4 samples at any one time to assist with selection.
Samples are designed to be large enough to provide a good example of the product, but small enough to be sent by A4 Envelope (First Class Royal Mail) to speed up the delivery process.
Please call 01666 504015 to order your free samples!
The term character can be applied in two ways with wood flooring. The first is referring to the aesthetic properties of the wood e.g. grain pattern, knots etc⌠the âcharacterâ of the timber. The other meaning of this term is as a grade description, i.e. âCharacter Gradeâ this denotes a way to visualise the grading specification. Character grade usually has a wider grain, with larger and more frequent knots permissible than a âselectâ grade, but not as much as a ârusticâ grade.
It is possible to fit wood floor planks to your wall. However, you should first double check for any relevant building regulations for the project youâre working on and the strength of the wall youâre fitting to.
This will depend on a number of factors unique to where the flooring is fitted. Typically, if the floor is well maintained and cleaned with the correct products, the finish should last for many years, possibly a lifetime depending on usage.
If a wood floor has not been properly maintained or is in a very heavy use environment, then you need to watch out for indicators that the finish is in need of maintenance. These indicators are typically:
How quickly the wood floor is getting dirty/how easy it is to clean any soiling off?
Does the wood feel rough? (not application to band sawn flooring)
Does the floor look patchy?
Has a chemical cleaner been used or spilt on to the floor?
If the answers to these questions are that it is hard to clean and looks/feels rough/patchy then it might be time to consider re-oiling. It is always best to get in touch with us first to discuss and sanding may not be required.
Generally speaking with wood flooring a tongue and groove system is better than click-lock. This because a tongue and groove system allow more flexibility in how the floor is fitted. A click-lock system is usually quicker to fit but if the click-lock mechanism is damaged during fitting it cannot be repaired unlike tongue and groove.
Yes â The samples will be representative of the colour, but Wood is a natural product. Therefore shade/colour variation, knotting and tightness of grain are all inherent characteristics.
We can guarantee that any product we manufacture from wood will contain such characteristics which will help to create your unique, individual and beautiful floor.
Random Lengths are standard lengths specified by The Solid Wood Flooring Company. These lengths are calculated to allow the best aesthetic variation in the finished floor. Typically the minimum length is 400mm and the maximum length is 1800mm. The overall average length is 900mm.
Fixed Lengths are stipulated for a particular product, with one or two layers in each carton split, with one half a minimum of 600mm long. This is designed to assist in fitting and minimise the need to sacrifice a longboard when cutting in.
Yes â We have a showroom at our Head Office in Tetbury, Gloucestershire. For more information please follow the link below;
Wood Flooring Showroom â Tetbury
We also have a permanent display at The Building Centre, London. This is an un-manned display, therefore if any assistance is required please call 01666 504015 and any one of our professional advisers would be more than happy to help. For more details please follow the link below;
Wood Flooring Display â The Building Centre (London)
Solid Wood Floor Boards are made by machining kiln dried timber to a regular size within fine tolerances.
Each plank is individual and will retain the characteristics of the tree that it came from, as every tree is individual. Solid Wood will react to changes in humidity and moisture and can move by more than 5% of its original kiln dried measurements.
This is why solid boards must be acclimatised prior to fitting and care must be taken when installing them. Always use a professional fitter!
Engineered boards are constructed from layers of Hardwood Ply and a final Solid Hardwood wear layer. These are Glued and Fused together in controlled factory conditions to produce a reliable, strong product. The Solid Wood Flooring Company use only the strongest backing and the construction of our boards are 8-11 layers of Cross-Ply Hardwood, with a final wearing layer of either 4, 5 or 6mm of Solid Wood. This produces a very stable board that is both load bearing and structurally sound. For more information, please call 01666 504015.
Not at all, the top layer of an Engineered Board is the same genuine Wood that you have in a Solid Board. The finished look of an Engineered Wood Floor will be identical to that of a Solid Wood Floor.
Sustainable Timber Flooring
We are very conscious of our environment and will only supply fully sustainable wood flooring. We are FSCŽ certified and PEFC⢠certified. This section reviews our ethical code of conduct and provides links to our certifications. If you have any more questions on our Responsible Purchasing Policy please call us on 01666 504 015.
Get in touch
Questions or comments? If you canât find the answer to your question on our site or want to leave some feedback, please fill in the form below.
Join our mailing list
Receive the latest news, offers and inspiration straight to your inbox.