Wood is the only renewable choice of building material for flooring. Plastics are derived from fossil fuels, concrete and other forms of flooring can damage our environment through the energy it takes for their production.
Wood is a renewable, natural resource that naturally grows in abundance. England was once covered by lush green forests.
Even though we’ve cut most of it down, our forefathers had the sense to replant large forests. Despite this, we don’t get a lot of our flooring from our own resources in the UK.
Most of our country’s Oak flooring now comes from Europe, including the extensive forests of North America.
All of these countries have programmes of replanting and maintaining sustainable forests. In many cases the Forest Stewardship Council® (FSC®) or PEFC™ certification helps to ensure that forest are responsibly managed.
Carbon Footprints
The production of wood flooring uses less energy in its processing methods than any other construction material.
For example, it takes 5 times more energy to produce 1 tonne of cement, 24 times more energy for 1 tonne of steel, and 126 times for 1 tonne of aluminium.
Young trees also absorb more carbon dioxide than mature ones, so it makes sense to harvest older trees and plant two new ones for every one tree felled.
This is why The Solid Wood Flooring Company is a member of the Timber Trade Federation
Engineered wood flooring should now be the only choice for any floor. This is because for every 100 m2 of solid wood flooring, you can get 400 m2 of engineered flooring.
The main positive points for using an engineered floor are:
- Engineered floors don’t move like solid wood floors
- We can produce 4 times as much engineered flooring, compared to solid oak floors
- Engineered flooring can be used with underfloor heating, whereas solid wood can’t
- The plywood base of an engineered floor is made up of layers of Birch and sometimes with a mix of Poplar
- Both of these fast growing trees are in abundance and are easily replaced, helping to reduce our carbon footprint even further
- Our engineered wood floors with a 5 mm solid top layer can be sanded down the same number of times as a solid wood floor. This is due the distance from the top of the tongue.
Our Certifications:
If you require a record of our ethical sourcing policies please see the links below for our certificates:
FSC Certificate
The Owners and Directors of The Solid Wood Flooring Company has made it a policy to only source from well managed legal sustainable forests and be responsible not only to the environment but also our clients, staff and contractors. We unreservedly condemn illegal logging and will not manufacture some exotic species as we believe that a lot are from questionable sources. With modern oiled finishes there are so many options that it seems a shame for companies to still sell flooring that comes from our ever reducing rain forest.
We only manufacture our own wooden flooring and can therefore control the sources of our raw material unlike a large number of our competitors who buy from traders.
We are FSC certified with a chain of custody certificate which means that all our FSC certified flooring can be traced back to the forest where it was harvested which ensures that it is responsibly managed. Further details can be found on the web site http://www.fsc.org/.
Our FSC Certificate is near to the bottom of this page: http://info.fsc.org/details.php?id=a0240000005sSKGAA2&type=certificate#result
We are also committed members of the Timber Trade Federation (TTF) and implement their Environmental Code of Practice and responsible purchasing policy (RPP). The RPP is a key issue in the timber industry today as it will ensure that all forests will eventually become totally sustainable, and over time the rain forest will get replanted. Further information can be obtained directly from the TTF web site at www.ttf.co.uk.
By following this policy we can ensure that for every tree harvested there will be more than one replanted. Never buy cheap wood flooring as it will invariably come from illegal logging operations where there is no management and locals cutting down trees and selling the raw material cheaply, in well managed forests only the best timber is selected.
The USA for example has always had a sustainable Forest Initiative as it has used timber in its house building and flooring in the early days of its evolution. The US has a regulatory framework enforces its good forestry practise throughout the US and Canada which is where our American White Oak, Walnut and Maple are sourced
form.
We are also very ecological in our manufacturing using off-cuts of Oak and walnut to manufacture our Sandwich Engineered Oak and fine line flooring. This means less wastage from the timber harvested.
The Solid Wood Flooring Company fully support the new regulations and we can demonstrate that we only source wood flooring products from legally logged sources, we have a Responsible Purchasing Policy in place and we have recently been independently audited by FSC and also by the Timber Trade Federation where we have a certificate for responsible purchasing
The following is what is happening:
- 3rd March 2013 a new European law called EUTR regulations comes into force and applies to anyone who places any timber product on the European market.
- The National Measurement Office (which is a government organisation) have been given the responsibility to check companies and ensure that they comply with the new European Regulations, and they already have a list of companies to target come the 3rd March.
What does the EUTR regulation mean?
It places the obligation on anyone who places any timber product on the European market, to ensure that the timber has been legally logged.
What is legally logged
A legally logged product is: Where the government of the country where the wood comes from, has given permission for the owner of the plantation and the logging company, to cut down the trees and sell them.
How can a purchaser check that the timber has been legally logged?
When the factories purchase their logs, they ask for certification from the seller of the timber, to confirm that the raw material has come from a legally logged source.
The operator – the person placing the finished product on the European market) will receive copies of that certification with all the other documents (certificate of Origin, Bill of Lading etc.,) when any shipment is delivered whether it is finished product or raw material.
As members of the Timber Trade Federation we have been following their Responsible Purchasing Policy for a long time and we can demonstrate that we have a chain of custody and the documentation to support that our raw materials come from legally logged sources.
If other companies don’t conduct the ‘Due Diligence’ that we have put in place then they will not be allowed to supply to anyone in Europe, and definitely not to any government projects in this country, and if they get caught placing illegally logged timber on the European market they can be penalised.
The penalties will be:
- Forced to stop trading.
- An unlimited fine.
- Up to 2 years in prison.
Forestry Stewardship Council FSC
As you know we are FSC accredited and our certification is on the FSC website in the International section. In some ways the EUTR regulation is trying to go farther than the FSC, but they will probably end up reflecting the same policies.
Timber Trade Federation
We are members of the Timber Trade Federation and support their policies. They are driving this new regulation.
The Programme for the Endorsement of Forest Certification (PEFC)
They are driving this new regulation.
Responsible Purchasing Policy (RPP)
This is a chain of custody created by the Timber Trade Federation to check where the timber comes from. We adopted this policy a long time ago and we have been operating it and have already been independently audited to check that we are doing it correctly and they are happy with us.
Why has this come about?
Activists from organisations such as Global Witness and Greenpeace have highlighted the worldwide problem and lobbied governments to try to stop illegal logging.
Countries like Malaysia (particularly the Sarawak region) have been placing illegally logged timber on the world market for a long time.
West Africa is also a concern and products such as Iroco and Wenge are high on the hit list.
The Wenge we supply has a PEFC certificate
Large banking companies have provided loans to illegal logging companies to enable them to operate.
Plywood is a big concern because of it’s construction and any ‘Mixed’ wood products are also a concern because of the construction of the backing such as multiply Birch or 3 ply Popular and these types of products are under scrutiny.
Brazil who were originally causing massive problems by stripping out the rain forests, have now largely cleaned up their act and although they are still cutting down the rain forests, the Brazilian Government has given the logging companies permission to cut the trees down! So they are not seen to be illegally logging!
In fairness, they are actually now planting far more trees than they cut down.
Natural oil is not cured by heat or by UV lamps it needs oxygen to cure and harden as we only use natural plant oils which are toy and child safe.
The oil is applied by soft rollers and run slowly through the finishing line to cure naturally. We then stack the boards to allow them to be fully dried and cured before packing.
Hard Wax oils can take longer to dry because they contain carnauba waxes, whereas natural plant oils, especially the new Heavy Duty Plus oil from Timberex will dry and cure much more quickly leaving the smooth wood with a silky texture and brushed boards with a beautiful enhanced finish.
Natural and Hard Wax Oils penetrate the wood’s cell structure helping to keep it natural looking and also very well protected. We can also apply coloured natural oils online like our E735 which has the Blanchon Maintenance Oil applied. This means that the colour goes all the way down into the cell structure and can easily be maintained and repaired using the same oil after installation, even after a few years. For high traffic areas this is important as corridors will get worn leaving the outside still looking new. By using oils we can just re-oil the worn parts making them look new again.
Maintenance of oiled floors is easy and in fact over time will be less costly than having to sand and re-lacquer floors.
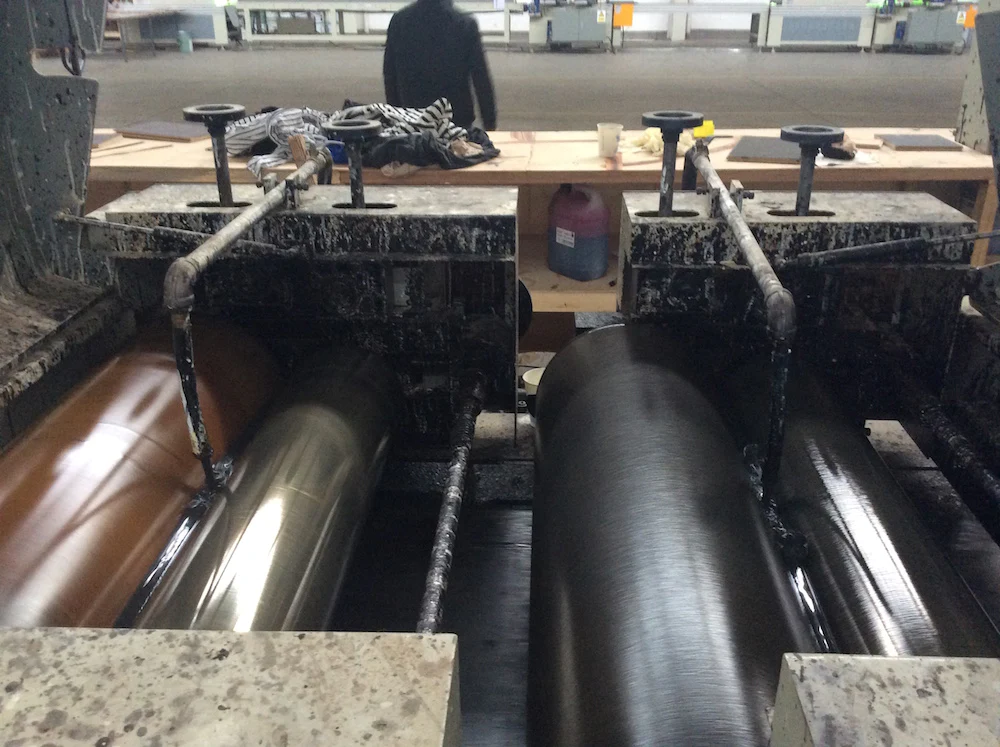
The part of the oiling line here has had lots of different colours used and we test a lot of new oils and finishes on this machine.
The oil is applied very accurately by adjusting the gap between the rollers, where the oil is pumped in and recirculated. The black roller on the right is the first one and is a soft roller, the second roller on the left is much harder and applies a second coat. The oil is then allowed to dry and little before another process down the line buffs the coloured oil into the grain and cell structure of the wood.
We can manufacture Oak skirting boards or Walnut skirting boards to any specific design. Some examples of how we have done this are shown below. We matched the band sawn finished flooring in Manhattan Loft Gardens with a solid Oak skirting because it was only 80mm high. You can also see how you can use our engineered skirting as a stair tread and riser as well. The large one is 240mm high x 2200mm long and 20mm thick with a solid 4mm veneer fumed and band sawn to match the chevron flooring going in the apartment hotel in central Manchester. Please call our team on 01666 504015 for further details and see how we can help you in the design and implementation of your projects.
Wood flooring is a visually appealing, environmentally friendly floor covering that can last for many years, when planned, fitted and cared for correctly.
Timber flooring must be fitted according to BS 8201:2011
For advice on how to work with the naturally occuring variations inherent with wood flooring please see our guide The Art of Fitting Wood Floors.
PLANNING:
Part of the planning process involves surveying the intended room in order to assure that the correct conditions are met. All wood is Hygroscopic, so as a material it will absorb moisture into its cell structure.
Before fitting your wood floor, it’s advisable to unpack 20% of the boards and lay them out to see the variation in grain and colour. Matching the knotting and shading is a big part of the fitting process.
A good, professional fitter will merge the colour variation in so the floor looks really natural with lighter and darker colours merging together. Alternatively, you may want all the light boards in one room and darker ones in other rooms, it’s all down to personal taste.
GENERAL CONSIDERATIONS:
Before you order your wood floor, it’s important to take the following points into consideration:
- What traffic the floor be exposed to
- What heat and moisture the floor will be exposed to
- Ensure all walls and floors are completely dry
- The substrate must be flat and smooth
- Fully test and regulate any underfloor heating
- Is it necessary to apply a moisture barrier or damp proof membrane to the substrate before fitting?
- Where will the boards be stored prior to fitting?
- Do the boards need acclimatising before fitting?
- Is the substrate dry?
FITTING YOUR BOARDS:
To minimise stress on the new boards, all substrates should be secure, dry, clean and level.
Allowances must be made for any movement either from the new floor or from the existing structure.
Depending on how the floor is fitted, and what other elements exist (such as underfloor heating), adequate time should be allowed for all elements such as adhesives or oils to mature before the floor is put into use.
Where solid boards are used, if the new floor exceeds 4 linear metres in any one direction, then extra provision for movement should be designed into the floor.
Where engineered boards are used, if the new floor exceeds 8 linear metres in any one direction, then extra provision for movement should be designed into the floor.
AFTER FITTING:
After fitting, your wood flooring should only be cleaned in the manner recommended by The Solid Wood Flooring Company.
Any items that will be sited on the finished wood floor, such as furniture, should have protective pads fitted to their feet to avoid potential damage to the oiled or lacquered finish.
Many people are unfamiliar with terms used in a particular industry, this blog is intended to help explain these phrases in a simple way, please let us know if you have any comments on these. There are a few blogs with separate headings on different aspects of wood flooring and fitting.
Acclimatisation
All solid wood flooring and Bamboo flooring should be placed in the room / environment where it is going to be fitted. In some cases where you have underfloor heating engineered wood flooring should also be acclimatised but can be fitted as soon as it is received if the conditions are normal. Every room or location has its own humidity levels and will depend on a lot of things. Acclimatisation means that wood flooring needs to get used to local humidity levels and heat. To acclimatise the boards correctly you should unpack them and allow the local air to circulate so that they can expand or contract and be stable prior to fitting. You should never acclimatise wood floors where there are still wet trades (wet trades means wet or damp plaster, damp concrete etc.)
Adhesives
These are the glues we use to fix the wood floor to the sub floor. Normally you would use the Bona R850 which we can supply along with a free notched trowel which can also be termed and applicator.
Architrave
This is a wooden trim to match your floor that goes around the door trim. If you have an existing one our fitters can use a special saw to cut underneath this trim to give a newly fitted, polished finish.
Batten
This is a piece of wood normally 25mm x 50mm or larger that supports the hardwood flooring so that you can secret nail the floor. In most cases you should glue directly to concrete or joists but batten can be used to take account of different level so that when you floor is installed it is all on one level.
Border
Our floor fitters can use contrasting materials such as white Oak and Walnut to create a border around the floor or in the middle.
Chipboard
This is a manmade board using small particles of wood as its main constituent. It is put in a high pressure press similar to the hot and cold press method used to make engineered flooring. Chipboard is one of the most common used subfloor as it is cheap but it is also very susceptible to damp. Leave it outside in the rain and it will disintegrate. Screws and normal nails will not work so if you use this as a sub floor you should glue the wood boards directly to this using Bona R850 adhesive. A better sub floor is bonded plywood.
Sandpaper Grit
Our floorboards are sanded to 120 grit and to put oil on the surface should be 120 grit to 180 grit. Grit is the coarseness of the sandpaper and 20 grit is very course with 180 grit being very smooth in comparison
Heart Wood
This is the hardest part of the tree and is normally darker than the outer rings of the tree and on a floor board will show as dark streak. With oils you can diminish this effect if you are trying to get a very uniform look.
Hygrometers
These instruments measure the moisture content of the air. To do this accurately you need a good quality instrument and it must be left in the area to be tested for at least 24 to 48 hours. Moisture from the surrounding walls (especially if they have been recently plastered) and also the sub floor exchanges with the air and this rate of exchange will depend on the ambient conditions prevailing at the time of the test. So to get accurate readings the device needs to be left so that it can get an accurate average reading. When installing a wooden floor to ensure that there are no problems in the future the relative humidity should be between 55% to 60% and the moisture content of the subfloor no more than 8%.
Insulation
This is often part of the subfloor but in old buildings you may not have this. If you have an old concrete floor always use BonaR410 or R580 to seal the top surface and keep any potential problem below not against the wood.
Joist
This is a structural beam that is used to support the upstairs floor or in old house the ground floor where there is a space under the ground floor with air bricks allowing air to circulate. The size of the joist will depend on when the house was built and also the loading it has to take. In old houses with air bricks the air circulated as we had open fires in these houses with central heating the floor boards will react more than they did in the old days which is why there are often large gaps as we like living in a hot house!
Latex Screed
You would use a latex screed if the concrete subfloor you were installing the wood floor on was uneven or unlevelled. These can sometimes be referred to as self-levelling compounds which is a liquid cement mix or where they add a paste or plastic to make the screed more flexible. These screeds can be anything for 3mm to 15mm thick and are normally quick drying. If you use such a levelling screed then we do not advise gluing the floor to this unless it is at least 12mm thick as it could lift from the original cement screed so please use these screeds with caution.
Damp Proof Membrane (DPM)
This is normally a plastic sheet that is impervious to water and moisture and is put below the cement screed before the cement is poured to stop any moisture going through the cement. It can get damaged so we also have a DPM on top of the cement such as Bona R410 or Bona R580 which are rubber type compounds that completely seal a floor to prevent any moisture from coming to the surface and gives you double protection. We always advise putting a DPM on top of a screed before fitting a floor because the last thing you want is for some moisture to creep through in a year and your nice wood floor lifts and warps and twists and does other nasty things that wood can do when subjected to too much moisture. In newer screeds the bottom of the screed will not have dried out anyway to the required level. The relative humidity in the screed needs to be less than 40% and the moisture content should be below 2%. If the wooden floor has a moisture content of 7% then the screed must be a lot lower than this.
Expansion and Expansion Gap
As wood is a hygroscopic material it will expand when it absorbs water or moisture and will also then contract when it loses it. However due to the cell structure and fibrous nature of wood once it expands it will never contract back to exactly the same size or shape which is why you can have cupped boards. When fitting a wooden floor even engineered you must always leave a gap around the perimeter at least 5mm for engineered boards and 10mm for solid wood. In the UK when we get humid weather the moisture content of wood flooring will be at its highest especially if doors and windows are left open, this means that the wood will absorb moisture and expand. In winter when we close all our doors and windows and turn up the central heating the humidity levels will be low so the wood will shrink, be careful not bring the humidity level below 20% otherwise you could cause serious damage to your wood floor even if you have engineered wood flooring. You should therefore air the house occasionally to maintain a natural environment.
Decibel Value and Sound Insulation
This is the measure of sound and our underlays have this in their specification. (Normally used in flats to prevent sound travelling to other apartments).
Face Nail and secret Nail: This is where you see the nail head on old floors that are in old buildings. Nails were normally punched below the surface and then filled and when they rust through you get dark patches on the surface of the floor. We now secret nail our boards thorough the tongue and groove but any solid board over 150mm wide should also have face nails otherwise with high humidity levels the boards could lift. This is why we only supply engineered boards wider than 150mm. BS8201:1987 states that boards exceeding 100mm in width should be fixed with surface nails we believe that secret screwing will be more than sufficient especially on our engineered boards up to 340mm wide.
Floating Floor
This is where the tongues and grooves are glued together using a PVA adhesive and the floor sits like a large slab on an underlay, so it ‘floats’ on top. This is not our preferred method of installation as it is always prone to problems. However with electric underfloor heating and some type of hot water system this is the only method that can be used Engineered boards can be floated but NEVER float a solid wood floor there be too movement.
Fillet
This is normally a thin piece of wood that is used on top of joists when they are not level
Noggin
This is a piece of timber that is fixed between joists so that it helps support the end of a board that spans the joists.
Floor sealer
This is a common term for varnish or lacquer to seal the surface this just sits on top of the wood.
Rising Damp
This happens when the membrane underneath a concrete screed or even in your foundations has failed and is cracked which will then allow moisture to rise up through the screed or walls. Moisture will always go to the driest part which is why we recommend adding a DPM on a screed even if it is perfectly dry and moisture free.
Scotia
This is a concave shaped wood floor accessory that is used like beading not something we recommend as you should always fit you floor under skirting boards.
Screed
This is the concrete floor that is your subfloor
Movement
This is the movement of your natural wood floor that will change throughout the seasons depending on humidity levels and heating conditions.
Nailer or Porta Nailer
Professional floor fitters’ use these nail guns to ensure that the secret nails go through the tongue at the correct angle and correct pressure. They can be either electric or air pressure operated. They can be easily hired form most tool hire companies.
Natural Oil
This is a modern product used to finish floors, the latest are VOC free and use natural substances that are environmentally friendly. Having research the market extensively we use Timberex wood oils. These are the best finishes and you can easily repair and maintain an oiled board.
Penny Joints
These can be termed washer joints due to the fact that there are very small gaps left between each floor board or every few boards for additional expansion. The term penny or washer was used because they used a thin washer or penny as a guide to make sure that each gap was equal. Due to modern manufacturing techniques and also the tolerances and moisture content of our wood flooring there is no need to use these now.
Sub floor
This is what you will install your wood flooring on to and is the floor below your final flooring finish.
T Moulding
This is shaped like a T-section and is used when you have a wooden floor that needs a gap between doorway (no need with our engineered boards) and where you go from a wood floor to carpet.
Screw and Plug
This method is where you have very wide boards and to ensure that they will not warp or twist we drill a hole just larger than the screw head just below the surface and then screw the board direct to joists or batten. Once fixed the top of the hole is then plugged with the same wood and sanded down so that you would not notice the hole once the wood floor has been finished.
Wood Flooring Underlay
These are manufactured specifically for wood flooring do not use a carpet underlay as they are not the same and could cause problems later.
Skirting Board
These are the boards that go on the wall above the wood flooring to cover up the bottom of the wall and the expansion gap you need to leave around the edge of the room. We manufacture these in lengths of 2100mm and also have matching skirting boards for all our flooring.
UV Cured
This is a method used at our factory to cure the oils and lacquers that we apply. This method cures the finish quickly but also ensures a much harder longer lasting finish than if you applied lacquers on site. We only use this for our lacquered and UV oiled pre-finished flooring.
Wax
These are old fashioned floor finishes and although they give lustre to the floor they are also not as hard wearing as modern oil finishes and we do not recommend using them.
Fitting a Floating Wood Floor
Cost Comparison of Floating or Fully Bonding a Wood Floor on a SR2 screed
A common question arises when considering the installation method of a plank-format wooden floor onto a screeded subfloor: Should you ‘float’ or ‘fully bond’?
Floating, refers to a method wherein an underlay is placed onto the subfloor and the wooden floor planks are laid on top of the underlay. Nothing is bonded to the subfloor, hence the term ‘floating’.
Fully bonded, on the other hand, is where the floorboards are glued directly to the screed – sometimes with an acoustic layer involved such as Regupol. Regardless, the boards are bonded to the subfloor.
In modern developments, most concrete screeds will be SR2 (SR stands for Surface Regularity), and some may even be worse than this. It is crucial to know and understand the SR value your screed achieves, as it will impact the performance of anything placed atop it and heavily factor into the chosen installation method.
Floating a wood floor, whether it is a click-lock or tongue and groove, requires an SR1 screed. Typically, this means applying a latex or self-leveling compound to the subfloor to ensure it is sufficiently level. Failure to do so can result in spongy or bouncy areas of the floor because the boards are effectively suspended between high points on the subfloor. Other issues can also occur such as squeaking along the joints due to the rubbing of the locking mechanisms (particularly noticeable on click-lock profiles) or lipping where the boards join.
To bring an SR2 (or below) screed up to SR1, the supply and install cost to complete a latex layer is normally around £10.00 + VAT per m2.
However, you can fully bond a wood floor to an SR1 screed. We always recommend fully bonding using our SW-890 MS Polymer adhesive; it is an industry leading adhesive with a very high shear strength. Our SW-890 MS Polymer adhesive can accommodate (spot level) variations in the floor of between 8mm to 10mm. The supply cost of this is around £5.00 per m2 (depending on the quantity ordered).
This means we can look at a side-by-side comparison of the two fitting methods. The labour costs are indicative and based on research from several leading contractors in late 2023:
Process | Floating | Fully Bonding |
Supply & Install Latex/Levelling | £10.00m2 | £0 |
Supply Underlay | £1.95m2 | £0 |
Supply T&G Adhesive | £0.21m2* | £0 |
Supply SW-890 Adhesive | £5.00m2** | |
Additional Labour | £2.00m2 | |
Total | £12.16 | £7.00m2** |
*Only required for T&G profiles
**Variable on volume ordered.
From the above, we can see that whilst floating can be initially inviting due to the low m2 cost of underlay and T&G adhesive; ultimately the cost in subfloor preparation makes fully bonding quicker and more cost effective when dealing with an SR2 screed.
Please note that parquet flooring (such as herringbone, chevron, weaves and panels) must be fully bonded to a suitable subfloor. For more information, please view our technical library.
If you would like to discuss any of the points within this document or have queries around your project, please get in touch via info@thesolidwoodflooringcompany.com or by calling +44 (0) 1666 504 015.
At The Solid Wood Flooring Company, we’re confident in the quality of all of our products. As manufacturers we sell only our own boards and do not supply our floors to retailers. Keeping our cliental close ourselves we can ensure you have expert advice and service throughout your decision process. Because you can’t see our products in a shop we cover the costs in sending sample pieces directly to you.
If you choose to use our free sample service, we’ll happily send out between 2 to 4 samples at a time. We will post out a full width board, 120mm long in an A4 envelope, first class. With that in mind, please note that if you do order more than 2 then they will be posted separately.
When ordering from our free sample service, please provide as much relevant information as possible. The following details will enable us to give you the best advice and service, as well as the correct product for your project.
- Full name and email address
- Name and address to where we should send the samples
- Telephone number
- Product code of samples required
- When will the wooden flooring be required?
- What is the subfloor? Concrete, old floorboards etc.
- Will there be underfloor heating? If so what type
- Any additional notes
Please note that whilst we are happy to provide samples we do not effect sales by sample. all sales of product are as per our product data sheets and are concluded upon our standard terms and conditions of business.
Architects & Designers
For architects and interior designers we are more than happy to send out a box of free samples to you. The standard box of samples comprises of 80 unique engineered wood floor samples and two product brochures. Please confirm the name of your practise and to whom we should send the samples as they will be sent by UPS usually on a next working day service. Please keep in mind that this package must be signed for.
We can also send out unique coloured oiled samples hand-finished in our Tetbury workshop. We’re always happy to try and match any colour swatch of what you provide us with and then can discuss producing the flooring to meet your exact requirements.
Just email us on info@thesolidwoodflooringcompany.com
Contractors
If you are trying to value engineer a project that has wood flooring or look at offering an alternative from what has been specified please contact us. As manufacturers we can make what you want at very competitive prices for the same product. We generally find we are sometimes more than 25% cheaper than a lot of our competitors due to our manufacturing and raw material sourcing abilities.
Call us between 8.30am to 5.30pm Monday-Friday and 9.30am to 12:30pm Saturdays and Bank Holidays to discuss your needs or simply fill in the contact form on the Contact Us page.