Download this page as a PDF document.
We are proud to release to the market our newest concept to further enhance our sustainability credentials, reducing wastage and upcycling previously unused cuts from our Oak trees. By using discarded branches and other off-cuts, we can create bespoke, handmade wall panels completely unique in character and design.
Each panel is 15mm thick with a 2mm End-Grain top layer, making it more stable and limiting any splitting. Splitting is a common characteristic of End Grain products given that they’re made out of a softer sapwood, and not the heartwood used for wood flooring. They react more noticeably to any change in humidity, so reducing the thickness makes them more flexible to these changes.
These intricate, handmade designs start from £97.50 per m2 and are normally supplied as unfinished, meaning that they can be treated on-site to meet the necessary fire regulations and achieve whatever colour and finish you desire.
Please call 01666 504015 for more information on the range of design options available to you.
PEFC (Pan European Forest Certification) is the world’s largest forest certification system and is internationally recognised benchmark in sustainability. As a top quality wood flooring manufacturer, we take ethical management of forests extremely seriously. We want you to be assured that when your buy flooring from us, that material has been stringently checked and responsibly sourced; to keep this information up to date we have annual audits to ensure accuracy and compliance.
You can check our PEFC Certification here or by searching Our certificate number: CATG-PEFC-400-AT at: www.pefc.org/find-certified.
View our PEFC Logo Usage Licence.
Sustainable Forest Management means the environmentally appropriate, economically viable and socially beneficial management for present and future generations. As scientific and ecological changes occur this certification system adapts and evolves to enable effective measures in maintaining our eco-system. PEFC is known for setting robust but realistic criteria for it’s forests and members. This diverse and adaptive model of certification gives PEFC the ability to avoid homogeneity and straight-jacketing into “one standard fits all”.
For more information on PEFC please visit www.pefc.org, for FSC certified information, please visit our specialist page: FSC Certified Wood Flooring.
In conjunction with Bona we have developed the highest slip resistant lacquered wood flooring in the UK market. 42 PTV in wet conditions, this is a factory finished product that will have a longer life than any on site application.
The finish has been used in a large number of restaurants and hotels and you can get a copy of the certificate to give to any local authority planning officer. You can be sure that this will meet their requirements and pass any extra stringent building regulations they may apply.
You will find most local authorities now will require the highest slip resistant possible and they have a requirement of a PTV value of 40 in the wet. Health and safety is now a major issue in any commercial environment and we have the highest PTV value in the wet rating on our wood floors.
Please download our PDF showing test results for slip resistance on lacquered flooring here.
For more information on grading and type testing please see our technical centre on type testing here.
There are other slip resistance flooring certificates for our various finished in the links below as we continually develop the latest finishes:
This floor has the highest slip resistance of any timber flooring with 45 PTV in the wet and 60 in the dry.
For more information on our certificates and other technical information please go here: Technical Library
We have the expertise to create sustainable wood flooring that will be accepted by local authority planning departments, English Heritage and the local Conservation Officer.
We have the expertise to create sustainable wood flooring that will be accepted by local authority planning departments, English Heritage and the local Conservation Officer.
Our E109 unfinished oak flooring for example has been approved as a replacement on many occasions and our E308 lacquered oak flooring has been used in lots of projects when refurbishing listed buildings.
If you are an Architect or interior designer then we can help with the NBS specification and provide samples for approval by English heritage and the local authority; this should help make planning approval a smooth process. Listed buildings can often be very difficult to work with, we are here to help!
We have found the link below very helpful for our individual clients.
http://www.english-heritage.org.uk/your-home/
Applying for Building Consent
Listed Building Consent is administered by your local planning authority or Council. Forms are available online or in hard copy if you visit your local office. It usually takes between eight and 13 weeks for a decision to be made, depending on the size and complexity of the proposal.
When a Council considers whether to grant or to refuse an application it must take into account the desirability of preserving the building, its setting and those features which make it special. Therefore you should consider those factors when planning your proposal for the changes to your property.
What should I do?
First, talk to your local conservation officer to check that you do need to make an application for Listed Building Consent. Then ask them to outline what might be acceptable and whether your ideas may need to be adapted to make them more likely to succeed.
If you have any questions regarding our wood floors and their suitability for your listed building, please call us on 01666 504015 or email info@thesolidwoodflooringcompany.com
Wood flooring is our only renewable choice for floors. Plastic is environmentally unfriendly coming from fossil fuels, concrete and other forms of flooring damage our environment with the energy required for their production.
Wood is a natural product that grows in abundance. England was once covered by forest and even though we cut most of it down our forefathers had the good sense to replant large forests although we do not now get a lot of our flooring from our own resources in the UK. Most of our Oak flooring now comes from Europe, the extensive forests of Russia, especially Siberia and North America.
All these countries have a programme of replanting and maintaining responsibly managed forests working with the Forest Stewardship Council (FSC) or other organisations to ensure we plant more trees that we cut down.
Carbon Footprints
The production of Wood Flooring uses less energy in its processing than any other construction material. For example it takes 5 times more energy to produce 1 ton of cement, 24 times for 1 ton of steel, and 126 times for 1 ton of aluminum. Young trees absorb more carbon dioxide than mature trees so it makes sense to harvest our older trees and plant two new ones for every one felled.
This is why we are members of the Timber Trade Federation and have a FSC chain of custody certificate.
- Engineered floors do not move like sold wood floors
- We can produce 4 times as much engineered floors compared to solid oak floors
- Engineered Flooring can be used with underfloor heating
- The plywood base is made up of layers of birch and sometimes with a mix of popular, both fast growing trees that are in abundance, and these trees are replaced helping to reduce our carbon footprint.
Our Wood Floors gain Top Marks from WWF
Here at the Solid Wood Flooring Company, we are delighted to have been awarded top marks from WWF UK for our sustainable wood sourcing efforts and environmental policies.
The WWF’s Timber scorecard sees companies rated for performance on using sustainable timber and timber products.
To raise awareness of the importance in tackling this agenda, and securing timber and timber products from responsible sources, the WWF are measuring the progress of timber and timber product buyers in the UK on sustainable sourcing.
The business community can play a vital role in ensuring forest resources are well-managed. Sustainable forest management can help redress some of the most severe problems affecting forests, such as deforestation. The use of recycled and reclaimed timber and wood fibres also makes a major contribution to consuming more wisely – and equitably, now and in the future.
We were awarded top marks of 3 trees – (a apt rating marker!)
By gaining three trees, the WWF found that The Solid Wood Flooring Company responded well to almost all of the requests WWF made regarding the purchasing of timber and timber products. We have made public commitments to using FSC certified and recycled timber and timber products, and to EUTR compliance, and have set up policies and control systems. The WWF’s found we report quantities openly and accurately and have a good understanding of the source of all our timber and timber products.
We are sourcing over 70% certified material, with high proportions of FSC certified and recycled timber and timber products. The Solid Wood Flooring Company are showing our competitors that it is possible to act responsibly when it comes to forest trade – but even we will need to find ways to do more to fulfil our targets by 2020.
We are delighted with the findings and are proud to support the WWF’s Save the Forests Campaign.
For more information on our Sustainability processes, FSC, PEFC and WWF Certifications, please visit our Technical Library
All of our engineered boards can be used for cladding walls or bar fronts and we are also able to manufacture to specific requirements if the size of order is sufficient which is normally over 1,000 m2
Click Here to see New Developments in Wall Panels and End-Grain
The contractor at the Old Spit Bank Fort selected out matching boards to clad the bar and then used the rest of our natural antique Oak E308L for the flooring and also cladding toilet areas and bedrooms.
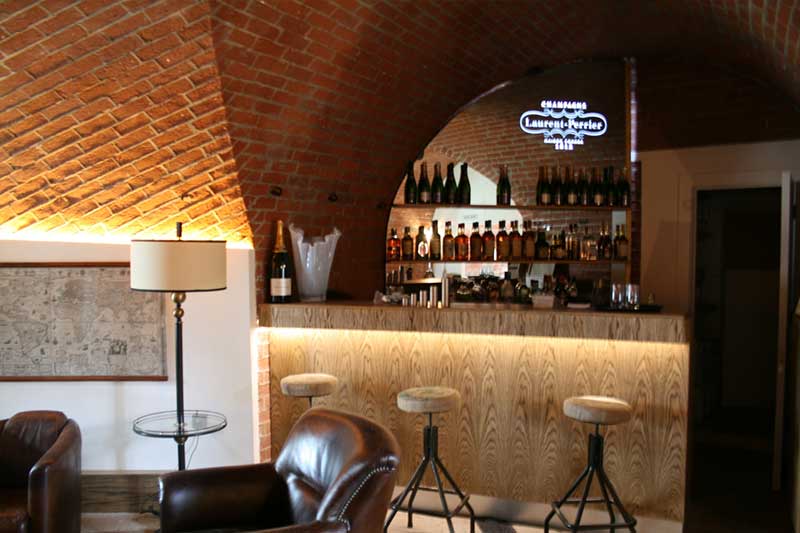
The image below is of one of the bedrooms as the engineered antique Oak was used extensively throughout the hotel and complemented the ancient Napoleonic Fort perfectly.
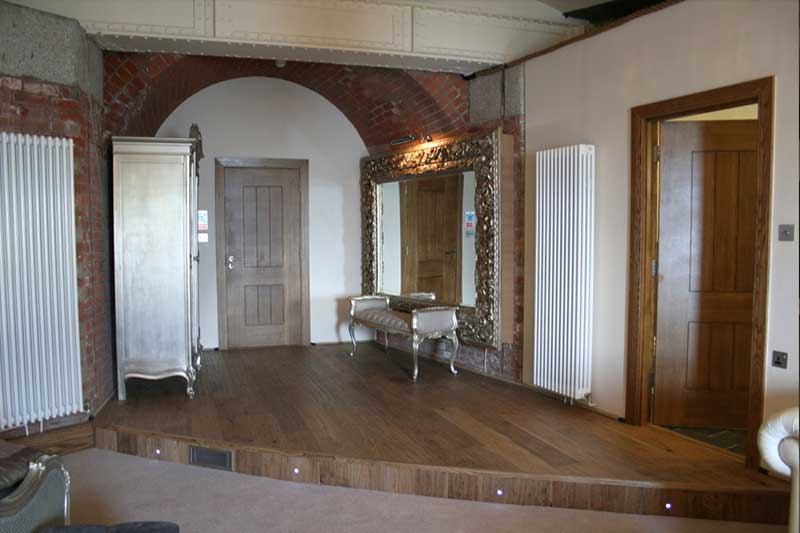
Oak, Maple, Walnut, Bamboo floor Specification Details
The Architects specification document (PDF) gives the full details of all our hardwood flooring ranges and products including finishes and fitting options. It also lists the accessories that can be used with the product code. When specifying just use the product code and indicate the fitting option you wish to use. You can see the colours of all the floors on the web site including fitted rooms and what lengths you can get in each of our cartons. Unlike the competition we do not supply cheap flooring with lots of short lengths. Random lengths are designed to give a room the old authentic look and it also allows us to manufacture more efficiently as we are able to use more of the tree.
Loading for Buildings
Our flooring meets all the requirements of BS 6399 part 1 for load bearing and we can confirm that our engineered and solid wood floors comply with BS 6399-1:1996 Table 1 section 3 and specifically Museum Floors and Art Galleries for exhibitions. It also complies with Clause 5.1.2 uniformly distributed loads and clause 5.1.3 Concentrated loads.
Carbonised Oak are ‘Thermo Floor Boards’ which have been heat treated to an extremely high temperature which removes all the moisture from the board so that the oak floor is totally stable. Our Carbonised Oak flooring is one of the best market and it is also engineered.
Engineered Oak Flooring is now one of the most popular wooden flooring options available due to its structure and sustainability. We get three times more wooden flooring from an engineered board than we do from a solid board. There is also no need to acclimatise before installation unless it is going over underfloor heating.
The Solid Wood Flooring Company manufactures unique products with the best managed forest timber products. We will not purchase or machine any timber from the rainforests, such as Teak etc. A good managed forest will plant more trees than it harvests and in North America, parts of Russia and even China this is very much the case. We do not have many of our deciduous forests left now so oak in the UK is in short supply. All our products are unique to us as they are made to our exacting specification and are British quality controlled.
We have two main manufacturing facilities specialising in our solid and engineered flooring range. The two main facilities are FSC certified to ensure that all our products are sourced ethically with the environment in mind.
Wooden flooring products are just like us, every tree is individual and unique as this is how nature works. The grain and colour variation on any single species of tree will be different, just like every human being is different. Even identical twins will have personality differences even though they may look alike. The seasons and climate changes will have an impact on trees and can alter their hue, colour and structure.
Advantages of our Product range
Over a period of years we have developed and extended our range of wooden flooring, many at the bequest of our Architect and Interior Designer clients. We place the most emphasis on quality and functionality and with no middlemen so you receive a top quality product at a reasonable price.
We are proud to offer you one of the largest ranges of solid and engineered wooden flooring in the UK market today.
The details below would be a typical specification for our American Engineered Walnut Flooring. The word document you can download here can be saved on your own computer, amended and copied and pasted to any specification, bills of quantity or as part of the design build contract. To get the full details of any product just enter the product code like E124 in the search facility and it will give you all you need to complete the document that you can download. Our Industrial finishes are the best.
Our grading and details of type testing of our hardwood floors can be found here.

Typical Specification used by NBS
K21 Wood strip / board / board fine flooring / linings – to be read with Preliminaries/General conditions.
TYPES OF FLOORING
110 WOOD BOARD FLOORING to T5 Hilton, 1 Poyle Road, Colnbrook, Slough. SL3 0EZ
Substrate: Cement and Sand Screed
- Preparation: Clean, Dry substrate with a moisture content of less than 10%
- Wood boards: Free from decay, through splits and insect attack (including ambrosia beetle damage, unless permitted in the class/ grade specified).
- Manufacturer: The Solid Wood Flooring Company – Tel: 01453 844 675 / mobile: 07831 680 206 / Email: info@thesolidwoodflooringcompany.com
Product reference: E502
- Species: Engineered American Walnut
- Appearance class/ Grade: To BS EN 942, ABCD Grade with sound knots up to 50mm permitted
- Board size: 190mm wide 21mm thick with a solid 6mm top layer in lengths of 1860mm with two boards 600mm plus
- Edges: Long edges tongued & grooved, Ends tongued & grooved.Bottom of long edges:
- Finish: Finished in WOCA natural oil – as delivered
- Moisture content at time of laying: 6-8%.
Laying: Flooring to be fitted in accordance with BS 8201:2011 Code of Practice for Flooring of Timber, Timber Products and wood based panel products
- Pattern: As laid.
- Adhesive: Bona R850 adhesive. Solid bed using 3mm notched trowel
- Method of finishing: Prefinished boards with builders clean.
- Other requirements:
- Expansion gaps: A 10mm expansion is gap required around the perimeter of the floor and/or where the wood flooring meets differing materials. 8mm expansion gaps should be designed into the floor at a minimum of 6 – 8 Lm in any one direction and construction joints should not be bridged.
- DPM: As designed into the floor
- Performance:
Load bearing: Conform to BS 6399-1: 1966 table 1 section 3
Reaction to fire: Perform to EN 13501-1 Dn s1 - Slip Resistance: Tested to BS 7967-2: 2002 (Pendulum Test) and achieve LOW Slip risk in the DRY and MODERATE risk in the WET
PREPARATION OF SUBSTRATES
210 DRYNESS OF CONCRETE/ SCREED SUBSTRATES
Relative humidity above substrate when tested with a hygrometer to BS 8201, Appendix A
(maximum): 75%.
- Test points: All corners, around perimeter, and random points over area being tested.
- Drying aids: Turned off for not less than 4 days before testing.
220 CONCRETE/ SCREED SUBSTRATES
Finished surface: Smooth, even, and free from abrupt changes in level. Apply suitable
smoothing compound, as necessary.
- Surface regularity when checked with a 3 m straightedge with 3 mm feet at each end, placed
- anywhere on the surface: No gap greater than 6 mm, and straightedge not obstructed by the
- substrate.
- Primer: If recommended by adhesive manufacturer, apply and allow to dry thoroughly before laying flooring.
590 PROTECTION
Protective covering: Submit proposals – Remove at completion.