Trees take CO2 from the atmosphere, capture it and produce oxygen in return. Wood provides shelter, comfort and beauty in our homes, offices, schools and public places. It protects our boundaries, opens new horizons in print and safely carries our goods around the globe.
For every tonne of CO2 a tree absorbs from the atmosphere nearly ¾ of a tonne of oxygen is produced*
Our forests are natural, highly efficient carbon sinks. Trees absorb and convert CO2 through photosynthesis into the nutrient sugars they rely upon and as a result of the process, oxygen is released.
Managed forests are the most efficient carbon sinks and producers of oxygen. The ongoing process of harvesting and replanting ensures there is always a healthy share of the forest made up of younger trees in vigorous growth. These absorb more CO2 than mature trees which left as they are in an unmanaged forest, eventually die and rot releasing carbon back into the atmosphere.
The CO2 absorbed by the tree during its life is trapped, or stored within the wood and remains so throughout the useful life of a wood product. The longer the life of that product the longer the CO2 is sequestered from the atmosphere. Repair, recycling and conversion to other types of wood based product can greatly extend the length of time carbon is stored.
Over 83% of the timber supplied in the UK is certified to be sustainable*
Of the remainder of timber not certified, the vast majority is well managed with due consideration to environmental and social issues. Certification and sustainable forest stewardship is growing incrementally around the globe: between 2005 and 2009 certification of all timber supplied in the UK grew by nearly 30%. The UK and Europe is most advanced in this process and over 98% of softwood used in Britain comes from here: its sustainability is evidenced by the growth of forest which is the equivalent to the area of Cyprus every year.
The industry which processes the harvested trees and ultimately manufactures wood products is extremely efficient. The UK and Europe’s sawn timber producers operate at, or very close to (average 97%), zero wastage of the wood extracted from the forest. Any material which cannot be used as solid wood is converted into wood chips for use in paper, particleboard, landscaping products or biomass fuel, which is often used by sawmills as an energy source.
Using wood instead of other building materials saves an average of 0.9 tonnes of CO2 per cubic metre.
A tonne of red brick for instance requires four times the amount of energy to produce than sawn timber, whilst concrete is five times less carbon efficient, steel 24 times and aluminium 126 times. By increasing the wood content of a building there is a proportional decrease in its carbon footprint. This is due to the extremely low energy consumption in the production of sawn timber and wood products in comparison with other building materials.
Factory production to the exact dimensions of timber frame structures contributes further to wood’s carbon advantage by dramatically cutting waste on site during the building process. In fact, it is possible to achieve CO2 reductions in the order of 88% on the build of a typical three bedroom detached house if softwood cladding is used in conjunction with a timber frame.
It costs around 5% less to build an energy efficient timber frame house or building*
Timber frame building has grown incrementally in the UK to an overall market share of around 25%. Lower build costs are a significant contributing factor to the increasing popularity of timber construction. Wood’s thermal insulation properties are 10 times better than brick and 5 times better than concrete. This adds up to a key cost advantage of timber construction in the achievement of reduced HLP (Heat Loss Parametre) when compared to masonry: the overall build cost savings range from 2.2% to 5.2% to achieve HLP compliances in the range of 1.3, 1.1 and 0.8.
Timber frame construction methods lead to a more efficient build process. Water tight within 5 days, a timber frame house is not subject to the traditional delay to other trades whilst the brickwork is finished. In comparison to wet construction methods there is little time lost due to drying out. Construction time on site is more predictable and 30% shorter with timber frame.
In its lifetime a uPVC window produces 1200% more CO2 than one made from wood*
Taking all material, production, transport and maintenance procedures into account wood is by far the least carbon intensive window material available. In production, uPVC’s oil base and the energy intensive smelting of aluminium contribute enormously to the carbon footprints of these materials. Wood’s exceptionally good natural insulating and cold-bridging properties are at least the equal of uPVC making it ideal in double and triple glazed applications.
Accelerated ageing tests simulating a range of environmental exposures have shown properly maintained, factory pre-coated units to have a life time in service similar to that of aluminium. uPVC units proved to be over 30% less durable. Uniquely, a wood window may also be economically repaired throughout its life. In these circumstances it is not uncommon for wood windows to last 100 years or so.
An ‘EUR’ wooden pallet stores around 29kg of CO2 taken from the atmosphere during the growth of the tree*
Pallets made from wood and wood derived packaging materials are the most carbon efficient option. Accounting for approximately 20% of European timber consumption these products are in most instances carbon neutral. Oil based PET, PVC and other plastics along with metals such as aluminium are significant net carbon contributors and remain so even once recycling is taken into account.
Heat treated wooden pallets have been shown by German researchers to be less susceptible to bacterial growth than those made of plastic. Wooden pallets conforming to ISPM 15 meet the most rigorous global hygiene standards and costs 50% less than the plastic alternative.
Once damaged a plastic pallet’s useful life is over. Wooden pallets are repairable, greatly extending their life and further reducing overall cost. When beyond service, wood pallets and packaging provide a substitute to fossil fuels if burnt as biomass to produce energy.
Change the materials you use not the climate. View Solid Wood Flooring Company’s Environmental Policy here.
Related News Stories
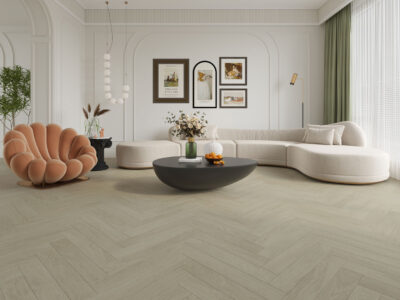
Laminate Flooring as a Smarter Specification Choice
Read more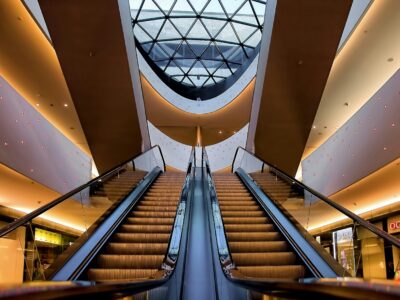
Is Laminate Flooring Suitable for Commercial Projects? What Architects and Contractors Need to Know
Read more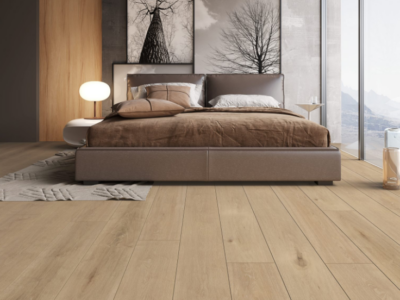
Industry insights: How Trident Laminate solves flooring challenges in high footfall environments
Read more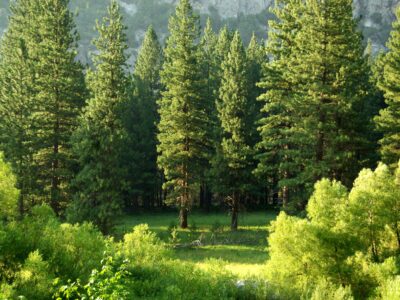
Why Developers Are Choosing Trident Laminate Flooring
Read moreJoin our mailing list
Receive the latest news, offers and inspiration straight to your inbox.